The annals of modern technology are rich with tales of innovation, yet few stories are as compelling as that of 3D printing, a process that translates digital blueprints into tangible objects, layer by meticulous layer. When I began this journey, I knew nothing about this technology. As the months progress, however, I see it as a world unto itself.
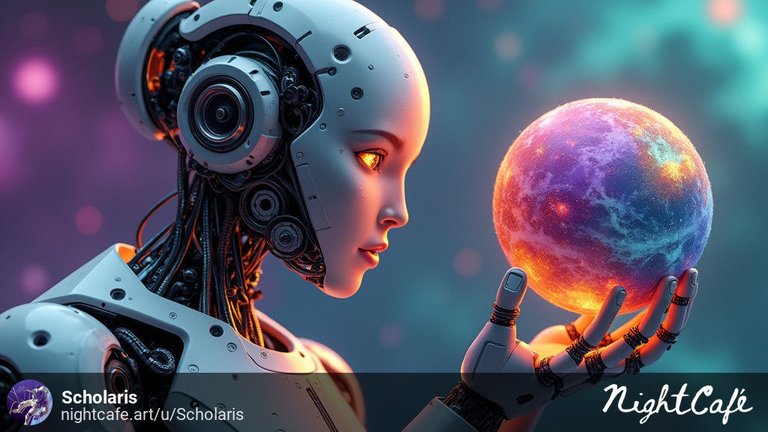
The Journey Begins
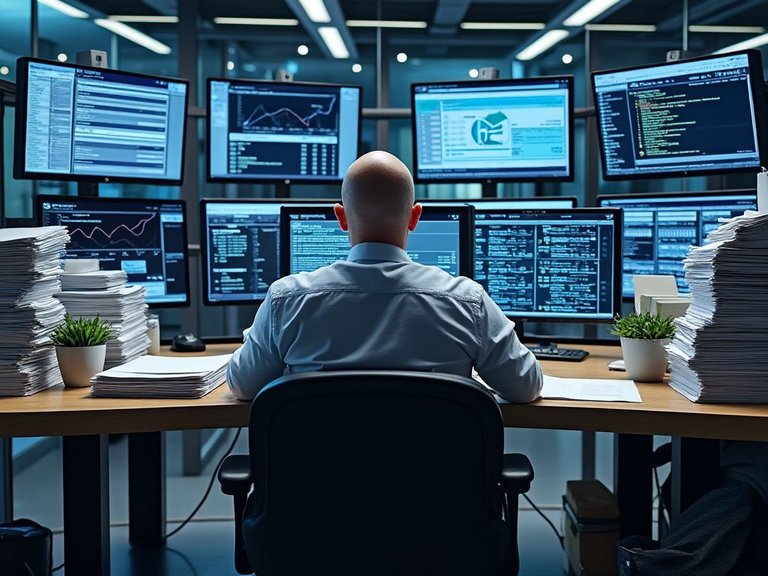
The most significant regulatory bodies within commercial nuclear power are the Nuclear Regulatory Commission (NRC) and the Institute for Nuclear Power Operations (INPO). From time to time, they direct power plants to evaluate various events to determine its applicability to their operations. If an event is applicable, the power station is expected to act. One day, an event came across my desk requiring a change to how I did business in the field of radiation protection.
Bruce Power
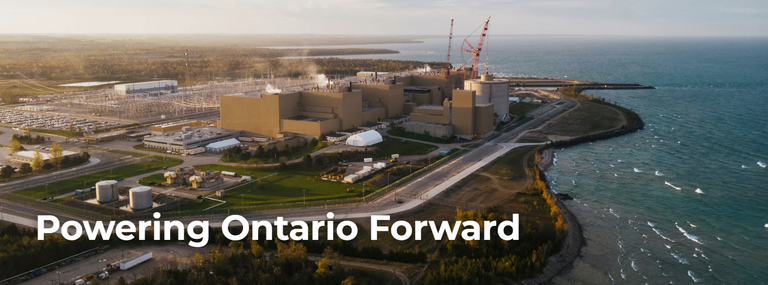
Health Physicists at Bruce Power were 3D-printing aficionados. They loved the activity and challenges of computer-automated drawings and printing physical objects. Their research discovered that materials were available for 3D printing that could reduce gamma and neutron radiation exposure. The problem, however, was that nuclear power plants had not yet utilized this technology in this manner. So, they took the initiative and started to build the platform I know of today.
Dragon's Fire
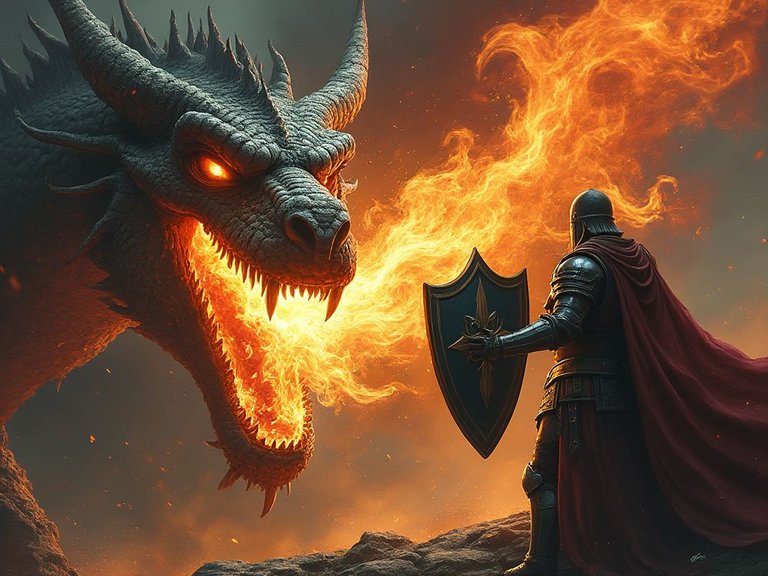
Akin to the hellish fire unleashed by a dragon, nature has a dragon's fire of its own in the form of radiation emitted by various materials. A wide variety of materials emit radioactive particles as they decay into a stable compound. A banana, for example, contains radioactive potassium and is relatively harmless to us. On the other hand, nuclear power plants contain materials that would sufficiently expose human beings to a degree that would require medical attention or concrete burial.
Radiation Shielding
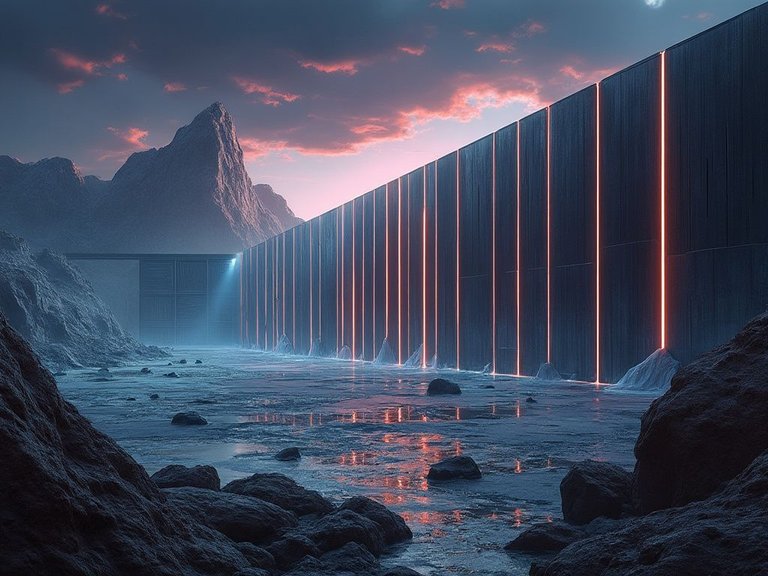
The basic premise of shielding is to put something between yourself and what can harm you. Regarding radiation protection, you must utilize materials capable of blocking small radioactive particles from reaching your body. In a nuclear power plant, this means identifying radiation sources and applying different materials to those sources before more people enter the area. For instance, a company like Eichrom NPO provides a wide range of materials that power plants can use to shield their workers from radiation sources.
3D printers, on the other hand, offer a new way to produce radiation shielding. Companies like Rapid 3D Shield and Add:North created plastic filaments embedded with materials like tungsten (gamma/neutron) and boron carbide (neutron). These filaments are fed into 3D printers to allow local onsite development of shielding materials of any shape but limited size.
Raise 3D Pro3 Plus High Speed
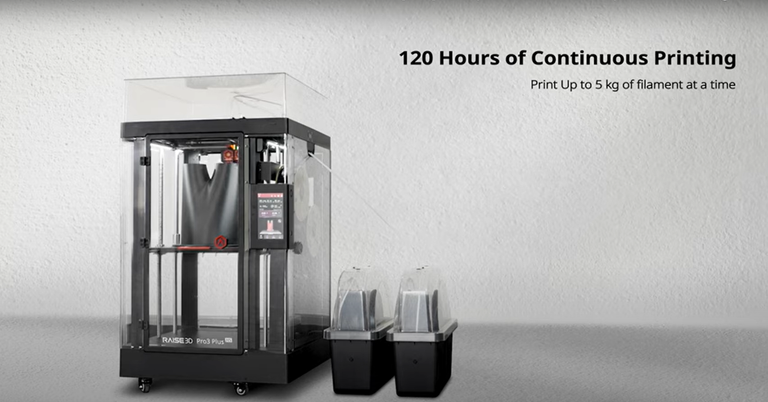
After reviewing several 3D printers on the market, I've decided to purchase two for work: the Raise 3D Pro3 Plus HS and the Bambu Lab X1E 3D. These will be used to print radiation shielding and other products on-site. Both printers are capable of using tungsten and boron carbide filaments for shielding. However, using only one printer would result in printing times exceeding 12 hours. I felt that for successful implementation of 3D printed radiation shielding, production time would need to be < 12 hours. Twelve hours is the typical length of a shift at work.
The shielding analysis would entail reviewing work orders within a particular area of the site. Technicians would perform radiation measurements to document surveys related to the planned maintenance. If shielding is required, I would determine the type, orientation, and amount needed.
If engineering analysis limits the amount of shielding needed for adequate exposure reduction, then laser-scanned measurements of the area are performed. These measurements then get fed into software like SolidWorks. From this point, the SolidWorks file is fed and edited into the 3D printer to generate the application I need for the field.
The Psyber X Multiverse
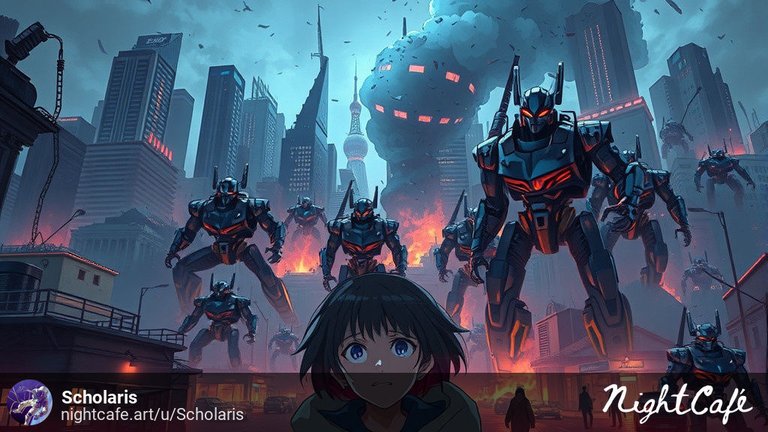
It's been a while since I've checked out the group at @psyberx. @bobthebuilder2 briefly discussed their development and remains confident in the group's progress. Having been a close part of their community during their initial introduction into the Hive community my faith remains strong and hopeful.
In my experience with project management, the beginning of any large project sucks. Having an idea form in your mind and seeing its creation is great. Maintaining it and further developing it with limited resources is where the rubber meets the road.
I look forward to what they bring in the future!
Join the @psyberx community today! Invest in their development or hop on to their discord to learn more about the initiative today!
In Closing
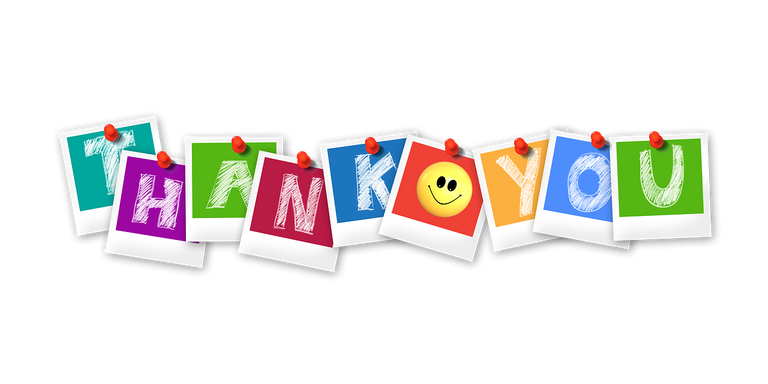
Thank you for reading and following on throughout my Hive journey. If you like this article, please consider reblogging, upvoting, and following @scholaris!
